
Destylacja rozpuszczalników to proces, który polega na oddzieleniu składników mieszaniny na podstawie różnicy w ich temperaturach wrzenia. Jest to technika szeroko stosowana w chemii, przemyśle farmaceutycznym oraz w produkcji alkoholi. Aby skutecznie przeprowadzić destylację, należy zrozumieć kilka kluczowych zasad. Po pierwsze, istotne jest, aby wybrać odpowiedni aparat destylacyjny, który może być prosty, jak kolumna destylacyjna, lub bardziej skomplikowany, jak destylator frakcyjny. Po drugie, temperatura wrzenia każdego ze składników musi być znana, aby można było ustalić optymalne warunki dla procesu. Warto również pamiętać o tym, że czystość rozpuszczalnika po destylacji zależy od liczby przeprowadzonych destylacji oraz od zastosowanej metody. Na przykład, w przypadku substancji o bliskich temperaturach wrzenia może być konieczne zastosowanie destylacji frakcyjnej, która pozwala na lepsze oddzielenie składników.
Jakie są najczęstsze zastosowania destylacji rozpuszczalników
Destylacja rozpuszczalników znajduje szerokie zastosowanie w różnych dziedzinach przemysłu oraz nauki. W przemyśle chemicznym jest kluczowym procesem wykorzystywanym do oczyszczania substancji chemicznych oraz separacji ich składników. Na przykład, w produkcji alkoholi etanol jest często wydobywany z fermentowanych surowców poprzez destylację, co pozwala na uzyskanie wysokiej jakości trunków. W laboratoriach chemicznych destylacja jest niezbędna do przygotowywania czystych reagentów oraz do usuwania zanieczyszczeń z próbek. Kolejnym ważnym zastosowaniem jest recykling rozpuszczalników organicznych, które mogą być wielokrotnie używane po odpowiedniej obróbce. Destylacja pozwala na odzyskiwanie tych substancji w sposób efektywny i ekonomiczny. W przemyśle petrochemicznym proces ten jest wykorzystywany do separacji różnych frakcji ropy naftowej, co umożliwia produkcję paliw oraz innych produktów chemicznych.
Jakie są różnice między destylacją a innymi metodami separacji
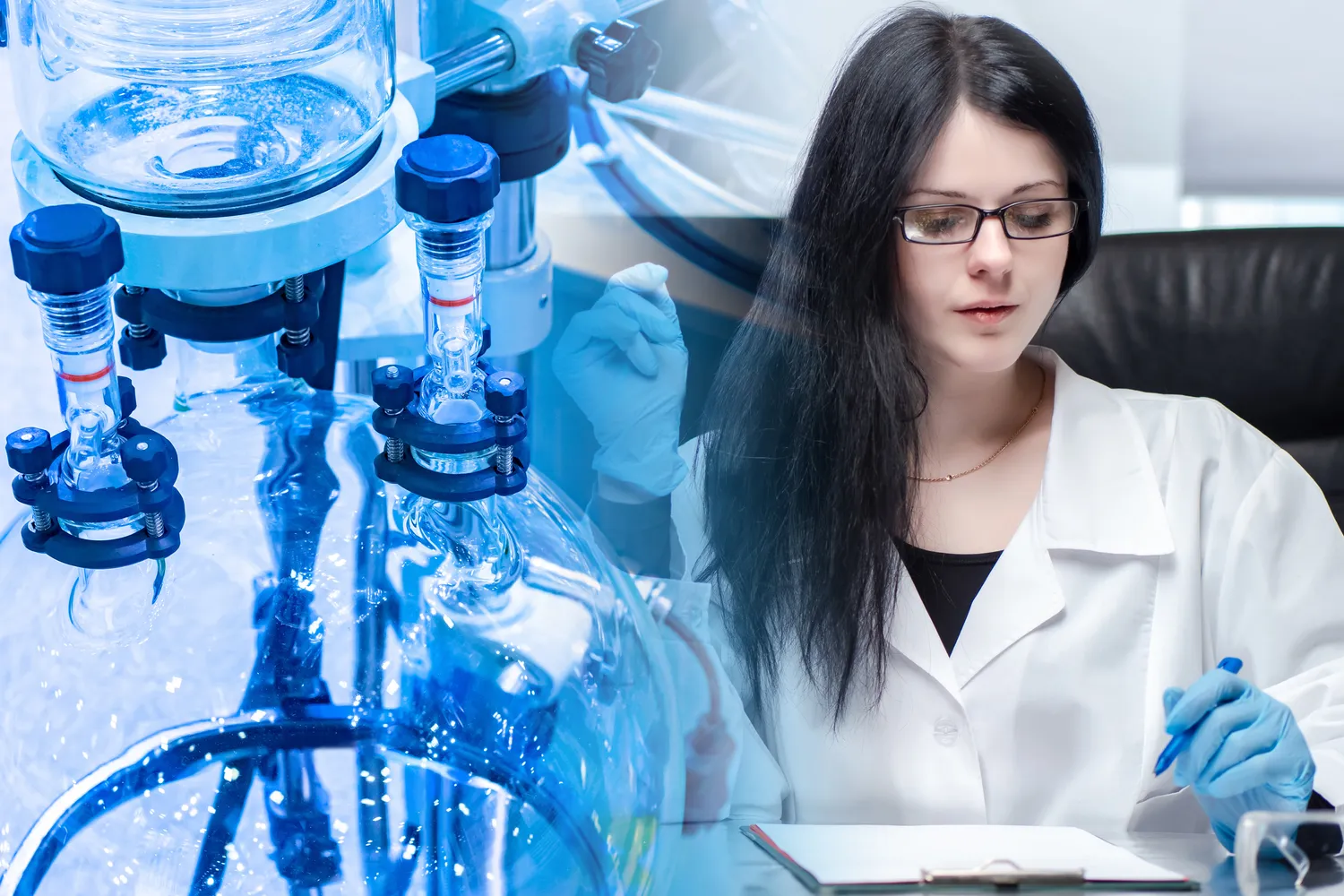
W kontekście separacji składników mieszanin chemicznych istnieje wiele metod, jednak destylacja wyróżnia się swoją specyfiką i zastosowaniami. Główna różnica między destylacją a innymi metodami polega na tym, że opiera się ona na różnicy temperatur wrzenia składników. W przeciwieństwie do filtracji czy ekstrakcji, które bazują na różnicach fizycznych lub chemicznych właściwości substancji, destylacja wykorzystuje zmiany stanu skupienia – przejście ze stanu ciekłego w gazowy i z powrotem w ciecz. Inną popularną metodą separacji jest chromatografia, która polega na rozdzielaniu składników mieszaniny na podstawie ich interakcji z fazą stacjonarną i ruchomą. Chociaż chromatografia może być bardziej precyzyjna w niektórych przypadkach, jej zastosowanie często wymaga drogiego sprzętu oraz skomplikowanych procedur. Destylacja natomiast jest bardziej dostępna i łatwiejsza do przeprowadzenia w warunkach laboratoryjnych oraz przemysłowych.
Jakie są najważniejsze czynniki wpływające na efektywność destylacji
Efektywność procesu destylacji rozpuszczalników zależy od wielu czynników, które mogą znacząco wpłynąć na jakość i ilość uzyskanego produktu końcowego. Pierwszym z nich jest temperatura wrzenia poszczególnych składników mieszaniny; im większa różnica między nimi, tym łatwiejsze będzie ich oddzielenie. Ważne jest również zachowanie odpowiednich warunków ciśnienia podczas procesu; obniżenie ciśnienia atmosferycznego może umożliwić przeprowadzenie destylacji w niższej temperaturze, co jest korzystne dla substancji termolabilnych. Kolejnym istotnym czynnikiem jest czas trwania destylacji; zbyt krótki czas może prowadzić do niedostatecznego oddzielenia składników, podczas gdy zbyt długi czas może skutkować degradacją niektórych substancji. Również jakość używanego sprzętu ma znaczenie; dobrze zaprojektowane aparaty destylacyjne mogą zwiększyć efektywność procesu poprzez lepsze zarządzanie przepływem pary i cieczy.
Jakie są różne rodzaje destylacji rozpuszczalników i ich zastosowania
W dziedzinie destylacji rozpuszczalników istnieje kilka różnych metod, które można zastosować w zależności od charakterystyki mieszaniny oraz oczekiwań dotyczących produktu końcowego. Najpopularniejszą formą jest destylacja prosta, która jest stosunkowo łatwa do przeprowadzenia i idealna dla mieszanin z wyraźnie różniącymi się temperaturami wrzenia. Proces ten polega na podgrzewaniu cieczy, a następnie skraplaniu pary, co pozwala na uzyskanie czystego składnika. Z kolei destylacja frakcyjna jest bardziej zaawansowaną techniką, która umożliwia separację składników o zbliżonych temperaturach wrzenia. W tym przypadku stosuje się kolumny frakcyjne, które zwiększają powierzchnię wymiany ciepła i pozwalają na wielokrotne skraplanie pary, co prowadzi do lepszego oddzielenia składników. Innym rodzajem jest destylacja azeotropowa, która jest stosowana w przypadku mieszanin tworzących azeotropy – substancje, które mają stały skład w określonej temperaturze wrzenia. W takim przypadku dodaje się substancję pomocniczą, aby zmienić właściwości azeotropu i umożliwić jego rozdzielenie.
Jakie są najważniejsze aspekty bezpieczeństwa podczas destylacji rozpuszczalników
Bezpieczeństwo podczas przeprowadzania destylacji rozpuszczalników jest kluczowym zagadnieniem, które należy wziąć pod uwagę zarówno w laboratoriach, jak i w przemyśle. Przede wszystkim należy pamiętać o odpowiednim przygotowaniu miejsca pracy; laboratoria powinny być wyposażone w wentylację oraz systemy odciągowe, aby zminimalizować ryzyko inhalacji szkodliwych oparów. Użytkownicy powinni nosić odpowiednią odzież ochronną, taką jak rękawice, okulary ochronne oraz fartuchy laboratoryjne, aby chronić się przed kontaktem z chemikaliami. Kolejnym istotnym aspektem jest kontrola źródeł ciepła; urządzenia grzewcze powinny być regularnie sprawdzane pod kątem sprawności oraz ewentualnych uszkodzeń. Należy również unikać przegrzewania cieczy, co może prowadzić do niebezpiecznych sytuacji związanych z gwałtownym wrzeniem czy eksplozjami. Warto także znać właściwości chemiczne używanych substancji; niektóre rozpuszczalniki mogą być łatwopalne lub toksyczne, co zwiększa ryzyko podczas ich obróbki.
Jakie są nowoczesne technologie wykorzystywane w destylacji rozpuszczalników
Nowoczesne technologie wykorzystywane w procesie destylacji rozpuszczalników stale się rozwijają, co przyczynia się do zwiększenia efektywności i bezpieczeństwa tego procesu. Jednym z innowacyjnych podejść jest zastosowanie technologii membranowych, które pozwalają na separację składników bez konieczności podgrzewania ich do wysokich temperatur. Dzięki temu można zaoszczędzić energię oraz zminimalizować ryzyko degradacji termicznej substancji. Innym ciekawym rozwiązaniem są systemy automatyzacji procesów destylacyjnych; nowoczesne aparaty wyposażone są w czujniki oraz oprogramowanie monitorujące parametry procesu w czasie rzeczywistym, co umożliwia precyzyjne dostosowywanie warunków pracy. Dodatkowo rozwój technologii nanomateriałów otwiera nowe możliwości w zakresie konstrukcji kolumn frakcyjnych oraz innych elementów aparatury destylacyjnej; materiały te mogą poprawić wydajność separacji dzięki zwiększonej powierzchni kontaktu między fazami. Warto również zwrócić uwagę na techniki zielonej chemii, które promują wykorzystanie mniej szkodliwych rozpuszczalników oraz procesów mniej obciążających środowisko naturalne.
Jakie są najczęstsze błędy popełniane podczas destylacji rozpuszczalników
Podczas przeprowadzania procesu destylacji rozpuszczalników można napotkać wiele pułapek i błędów, które mogą negatywnie wpłynąć na jakość uzyskanego produktu oraz efektywność całego procesu. Jednym z najczęstszych błędów jest niewłaściwe ustawienie temperatury grzania; zbyt niska temperatura może prowadzić do niedostatecznego oddzielenia składników, natomiast zbyt wysoka może skutkować ich degradacją lub niepożądanym reakcjom chemicznym. Kolejnym powszechnym problemem jest niewłaściwe dobranie aparatury destylacyjnej; użycie niewłaściwego typu kolumny lub destylatora może znacząco obniżyć wydajność procesu. Ponadto brak odpowiedniego monitorowania parametrów pracy może prowadzić do nieprzewidzianych sytuacji, takich jak przegrzanie czy nadmierna produkcja pary. Ważnym aspektem jest również ignorowanie zasad bezpieczeństwa; wiele incydentów wynika z braku odpowiednich środków ochrony osobistej lub niewłaściwego przygotowania miejsca pracy.
Jakie są korzyści ekonomiczne wynikające z zastosowania destylacji rozpuszczalników
Zastosowanie destylacji rozpuszczalników przynosi wiele korzyści ekonomicznych zarówno dla przemysłu chemicznego, jak i dla mniejszych laboratoriów badawczych. Po pierwsze, proces ten pozwala na odzyskiwanie wartościowych substancji chemicznych z mieszanin, co przyczynia się do zmniejszenia kosztów zakupu nowych surowców. Efektywna separacja składników pozwala na maksymalne wykorzystanie dostępnych materiałów i minimalizację strat surowców. Ponadto inwestycja w nowoczesne aparaty destylacyjne może przynieść długoterminowe oszczędności dzięki zwiększonej wydajności procesu oraz redukcji zużycia energii. W wielu przypadkach automatyzacja procesów destylacyjnych pozwala na zmniejszenie kosztów pracy poprzez ograniczenie potrzeby ciągłego nadzoru nad operacjami. Dodatkowo stosowanie metod ekologicznych w procesach destylacyjnych może przyczynić się do obniżenia kosztów związanych z przestrzeganiem norm środowiskowych oraz kar za zanieczyszczanie środowiska.
Jakie są przyszłe kierunki badań nad destylacją rozpuszczalników
Przyszłość badań nad destylacją rozpuszczalników zapowiada się obiecująco dzięki ciągłemu postępowi technologicznemu oraz rosnącemu zainteresowaniu ekologicznymi aspektami procesów chemicznych. Wśród najważniejszych kierunków badań można wyróżnić rozwój nowych materiałów dla aparatów destylacyjnych; nanotechnologia oferuje możliwość stworzenia bardziej efektywnych kolumn frakcyjnych czy membran separacyjnych o zwiększonej powierzchni kontaktu między fazami. Dodatkowo badania nad alternatywnymi metodami separacji mogą prowadzić do opracowania bardziej ekologicznych technologii, które będą mogły zastąpić tradycyjne metody destylacyjne w przypadku trudnych mieszanin chemicznych czy substancji toksycznych. W kontekście zmian klimatycznych coraz większą uwagę przykłada się także do efektywności energetycznej procesów przemysłowych; badania nad optymalizacją warunków pracy aparatów destylacyjnych mogą przyczynić się do znacznego zmniejszenia zużycia energii i emisji gazów cieplarnianych.