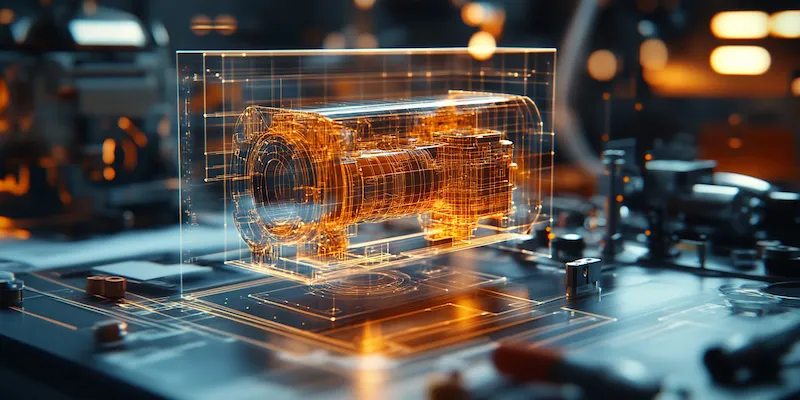
Budowa maszyn pneumatycznych opiera się na kilku kluczowych elementach, które współdziałają ze sobą w celu efektywnego przetwarzania energii pneumatycznej. Podstawowym komponentem jest sprężarka, która odpowiada za wytwarzanie sprężonego powietrza. Sprężarki mogą być różnego rodzaju, w tym tłokowe, śrubowe czy wirnikowe, a ich wybór zależy od specyfiki zastosowania. Kolejnym istotnym elementem są zbiorniki ciśnieniowe, które przechowują sprężone powietrze i umożliwiają jego późniejsze wykorzystanie. W systemach pneumatycznych niezbędne są również zawory sterujące, które regulują przepływ powietrza i kontrolują pracę poszczególnych komponentów. Ważnym aspektem budowy maszyn pneumatycznych są także siłowniki, które przekształcają energię pneumatyczną w ruch mechaniczny. Siłowniki mogą mieć różne konstrukcje, w tym cylindry jednostronnego lub dwustronnego działania. Oprócz tego nie można zapomnieć o elementach zabezpieczających, takich jak filtry czy zawory bezpieczeństwa, które chronią system przed nadmiernym ciśnieniem oraz zanieczyszczeniami.
Jakie zastosowania mają maszyny pneumatyczne w przemyśle
Maszyny pneumatyczne znajdują szerokie zastosowanie w różnych gałęziach przemysłu, co czyni je niezwykle wszechstronnymi narzędziami. W przemyśle produkcyjnym wykorzystywane są do automatyzacji procesów montażowych oraz pakowania, co znacznie zwiększa wydajność pracy. Dzięki swojej niezawodności i szybkości działania maszyny te idealnie sprawdzają się w liniach produkcyjnych, gdzie czas reakcji ma kluczowe znaczenie. W branży spożywczej maszyny pneumatyczne są używane do transportu surowców oraz pakowania produktów, co zapewnia wysoki poziom higieny i bezpieczeństwa. W sektorze motoryzacyjnym ich zastosowanie obejmuje zarówno montaż części, jak i testowanie komponentów pod kątem jakości i wytrzymałości. Ponadto maszyny pneumatyczne znajdują zastosowanie w budownictwie, gdzie służą do obsługi narzędzi ręcznych oraz urządzeń ciężkich. Dzięki swojej elastyczności i możliwości łatwego dostosowania do różnych warunków pracy, maszyny te stają się coraz bardziej popularne w różnych dziedzinach przemysłu.
Jakie są zalety i wady maszyn pneumatycznych

Maszyny pneumatyczne charakteryzują się wieloma zaletami, które przyciągają uwagę inżynierów oraz menedżerów produkcji. Jedną z głównych korzyści jest ich prostota konstrukcji oraz łatwość obsługi, co sprawia, że są one dostępne dla szerokiego kręgu użytkowników. Dodatkowo maszyny te cechują się dużą niezawodnością oraz niskimi kosztami eksploatacji, co czyni je atrakcyjnym rozwiązaniem dla wielu przedsiębiorstw. Pneumatyka pozwala na osiąganie dużych prędkości pracy przy jednoczesnym zachowaniu wysokiej precyzji działania. Jednakże istnieją również pewne ograniczenia związane z używaniem maszyn pneumatycznych. Wśród nich można wymienić konieczność stosowania sprężonego powietrza jako źródła energii, co wiąże się z dodatkowymi kosztami związanymi z jego wytwarzaniem oraz dystrybucją. Ponadto systemy pneumatyczne mogą być mniej efektywne w porównaniu do hydraulicznych w przypadku aplikacji wymagających dużej siły lub precyzyjnego sterowania ruchem. Warto również zauważyć, że maszyny te są często bardziej podatne na awarie związane z zanieczyszczeniem powietrza czy uszkodzeniami mechanicznymi.
Jakie innowacje wpływają na rozwój maszyn pneumatycznych
W ostatnich latach obserwuje się dynamiczny rozwój technologii związanej z budową maszyn pneumatycznych, co przekłada się na ich coraz szersze zastosowanie w różnych branżach przemysłowych. Innowacje te obejmują zarówno nowe materiały konstrukcyjne, jak i zaawansowane systemy sterowania oraz automatyzacji procesów. Dzięki zastosowaniu lekkich i wytrzymałych materiałów możliwe stało się zmniejszenie masy urządzeń przy jednoczesnym zwiększeniu ich efektywności energetycznej. Wprowadzenie inteligentnych systemów monitorowania pozwala na bieżące śledzenie parametrów pracy maszyn oraz szybką diagnostykę ewentualnych usterek, co znacząco zwiększa niezawodność całego systemu. Również rozwój technologii Internetu Rzeczy (IoT) umożliwia integrację maszyn pneumatycznych z innymi urządzeniami w zakładzie produkcyjnym, co prowadzi do większej automatyzacji procesów i optymalizacji produkcji. Nowoczesne algorytmy sterowania pozwalają na precyzyjne zarządzanie pracą siłowników oraz zaworów, co przekłada się na lepszą wydajność energetyczną i mniejsze zużycie mediów.
Jakie są kluczowe zasady projektowania maszyn pneumatycznych
Projektowanie maszyn pneumatycznych wymaga uwzględnienia wielu kluczowych zasad, które mają na celu zapewnienie ich efektywności oraz bezpieczeństwa użytkowania. Przede wszystkim należy zwrócić uwagę na odpowiedni dobór komponentów, takich jak sprężarki, zbiorniki czy siłowniki, które muszą być dostosowane do specyficznych wymagań aplikacji. Ważne jest również, aby systemy pneumatyczne były zaprojektowane z myślą o łatwej konserwacji i serwisowaniu, co pozwoli na minimalizację przestojów w produkcji. Kolejnym istotnym aspektem jest analiza obciążeń oraz warunków pracy, co pozwala na określenie odpowiednich parametrów roboczych, takich jak ciśnienie czy przepływ powietrza. Warto również pamiętać o zastosowaniu elementów zabezpieczających, takich jak zawory bezpieczeństwa czy filtry, które chronią system przed uszkodzeniami spowodowanymi nadmiernym ciśnieniem lub zanieczyszczeniami. Dobrze zaprojektowane maszyny pneumatyczne powinny być również ergonomiczne, co oznacza, że ich obsługa powinna być intuicyjna i komfortowa dla operatorów.
Jakie są najczęstsze problemy związane z maszynami pneumatycznymi
Maszyny pneumatyczne, mimo swoich licznych zalet, mogą napotykać różnorodne problemy podczas eksploatacji. Jednym z najczęstszych kłopotów jest nieszczelność układu pneumatycznego, która może prowadzić do utraty ciśnienia i obniżenia wydajności całego systemu. Nieszczelności mogą występować w różnych miejscach, takich jak połączenia rur czy uszczelnienia zaworów. Innym problemem są zanieczyszczenia sprężonego powietrza, które mogą prowadzić do uszkodzenia komponentów oraz obniżenia jakości pracy maszyn. Dlatego tak ważne jest stosowanie filtrów oraz regularne czyszczenie systemu. Awaria sprężarki to kolejny istotny problem, który może spowodować zatrzymanie całej produkcji. Warto również zwrócić uwagę na zużycie elementów roboczych, takich jak siłowniki czy zawory, które wymagają regularnej wymiany lub regeneracji. Problemy z kontrolą ciśnienia to kolejny aspekt, który może wpłynąć na działanie maszyn pneumatycznych. Zbyt wysokie lub zbyt niskie ciśnienie może prowadzić do nieprawidłowego działania urządzeń oraz zwiększonego ryzyka awarii.
Jakie są trendy w rozwoju technologii maszyn pneumatycznych
W ostatnich latach można zaobserwować szereg trendów wpływających na rozwój technologii maszyn pneumatycznych. Jednym z nich jest rosnące zainteresowanie automatyzacją procesów przemysłowych, co prowadzi do większego zastosowania robotyki w połączeniu z systemami pneumatycznymi. Dzięki integracji tych dwóch technologii możliwe jest osiągnięcie wyższej wydajności oraz precyzji w produkcji. Kolejnym trendem jest rozwój inteligentnych systemów sterowania opartych na sztucznej inteligencji i uczeniu maszynowym, które pozwalają na optymalizację pracy maszyn oraz przewidywanie ewentualnych awarii. Wprowadzenie Internetu Rzeczy (IoT) do przemysłu umożliwia zdalne monitorowanie stanu maszyn oraz ich parametrów pracy w czasie rzeczywistym, co znacząco zwiększa efektywność zarządzania produkcją. Ponadto coraz większą uwagę przykłada się do kwestii ekologicznych i efektywności energetycznej systemów pneumatycznych. Producenci dążą do opracowywania rozwiązań zmniejszających zużycie energii oraz emisję hałasu związanych z pracą maszyn. Warto także zauważyć rosnącą popularność materiałów kompozytowych i lekkich stopów metali w budowie komponentów pneumatycznych, co przyczynia się do redukcji masy urządzeń i ich większej mobilności.
Jakie są koszty związane z budową i eksploatacją maszyn pneumatycznych
Koszty związane z budową i eksploatacją maszyn pneumatycznych mogą być bardzo zróżnicowane i zależą od wielu czynników. Na etapie budowy kluczowe znaczenie ma wybór odpowiednich komponentów oraz ich jakość. Sprężarki, zbiorniki ciśnieniowe czy siłowniki różnią się ceną w zależności od producenta oraz zastosowanej technologii. Dodatkowo należy uwzględnić koszty instalacji oraz uruchomienia systemu, które mogą być znaczne w przypadku bardziej skomplikowanych rozwiązań. Koszty eksploatacyjne obejmują zarówno zużycie energii elektrycznej potrzebnej do pracy sprężarek, jak i wydatki związane z konserwacją oraz serwisowaniem maszyn. Regularne przeglądy techniczne są niezbędne dla zapewnienia niezawodności i długowieczności urządzeń, co wiąże się z dodatkowymi kosztami. Należy także pamiętać o kosztach związanych z zakupem mediów eksploatacyjnych, takich jak oleje czy filtry powietrza. Warto jednak zauważyć, że inwestycja w maszyny pneumatyczne często przynosi długofalowe oszczędności dzięki zwiększeniu wydajności produkcji oraz redukcji kosztów pracy.
Jakie są przyszłe kierunki rozwoju technologii pneumatycznej
Przyszłość technologii pneumatycznej rysuje się w jasnych barwach dzięki ciągłemu postępowi technologicznemu oraz rosnącym wymaganiom rynku przemysłowego. Jednym z głównych kierunków rozwoju będzie dalsza automatyzacja procesów produkcyjnych poprzez integrację systemów pneumatycznych z robotyką i sztuczną inteligencją. Dzięki temu możliwe będzie osiągnięcie jeszcze wyższej wydajności oraz precyzji operacji przemysłowych. Ponadto rozwój Internetu Rzeczy (IoT) otworzy nowe możliwości monitorowania stanu maszyn w czasie rzeczywistym oraz analizy danych dotyczących ich pracy, co pozwoli na lepsze zarządzanie procesami produkcyjnymi i szybsze reagowanie na ewentualne awarie. W kontekście ochrony środowiska coraz większy nacisk kładzie się na efektywność energetyczną systemów pneumatycznych oraz minimalizację ich wpływu na środowisko naturalne poprzez stosowanie bardziej ekologicznych materiałów i technologii produkcji. Również rozwój materiałów kompozytowych i lekkich stopów metali przyczyni się do zmniejszenia masy urządzeń oraz poprawy ich mobilności i wszechstronności zastosowań.